SECTOR
MOST FLEXIBLE PACKAGING, MANY OF WHICH FIND APPLICATION IN THE FOOD INDUSTRY, ARE MADE THROUGH PRINTING AND COUPLING/LAMINATION PROCESSES; THESE PROCESSES ALLOW YOU TO COUPLE MORE FLEXIBLE FILMS AND GUARANTEE THE WELL PRECISE TECHNICAL FEATURES ABLE TO PRESERVE THE CHARACTERISTICS OF THE PRODUCT THAT WILL BE CONTAINED OVER TIME.
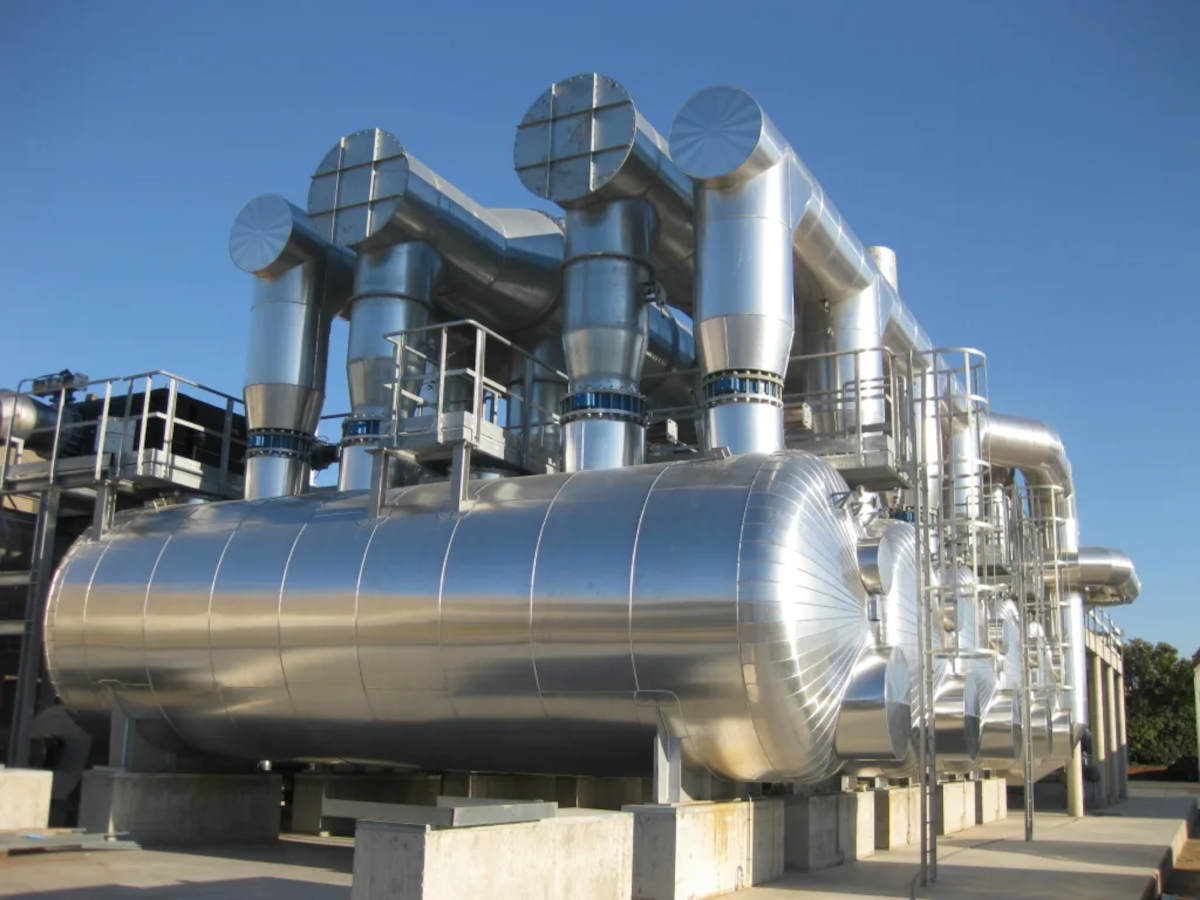
PRINTING SECTOR – THE ENVIRONMENTAL IMPACT
All the printing and laminating processes that use solvent-based inks and glues, provide a drying phase of the printed / laminated film. During this phase the solvent contained in the inks, in the adhesives, necessary for their dilution, is emitted into the atmosphere from the drying sections (ovens) of the printing / laminating machines.
EMISSIONS CHARACTERISTICS
Air emissions from flexible film printing and laminating processes have the following characteristics:
VARIABLE | CHARACTERISTICS |
---|---|
Temperature | 40-70°C, depending on the print support used |
Presence of volatile organic compounds (V.O.C.) | Alcohols and esters (acetates) |
Flow rates of emitted air | More or less high, depending on the number of printing and laminating machines present, and their characteristics |
Operational cycle | On several daily shifts |
Variability | High, depending on the simultaneity of the machines in operation, and the applied colour and quantity of the relevant printing / coating band |
DEPURATION GOALS
Depuration goals are mainly to reduce the emissions into the atmosphere of pollutants harmful to the environment (V.O.C.s), allowing compliance with the regulatory limits for all present pollutants, and allowing the recovery and reuse of the solvent necessary for the dilution of inks and adhesives.
THE SOLUTION THROUGH THE PROCESS OF ADSORPTION ON ACTIVATED CARBON AND REGENERATION WITH INERT GAS
To solve the environmental problem, characterized by emissions with very variable air flow characteristics and considerable solvent mass flows (350 kg / h initially, 700 kg / h after subsequent expansion of the plant), an activated carbon solvent recovery plant was installed, with inert gas regeneration.
The choice of using inert gas (nitrogen, in this specific case) was made to maximize the recovery of the solvents present, which are partially or totally soluble in water; the plant, therefore, allows to avoid the production of aqueous liquid wastewater to be disposed of. The recovery of the solvents takes place in conditions of total safety, as nitrogen is used to remove the solvent accumulated by the activated carbons, makes the environment inert and therefore avoids any risk of explosiveness.
THE MEASURES IDENTIFIED FOR APPLICATION IN THE FLEXIBLE PACKAGING INDUSTRY
SOLVENT RECOVERY IS A PROCESS FREQUENTLY USED FOR THE TREATMENT OF ATMOSPHERIC EMISSIONS CONTAINING V.O.C.s RELEASED IN THE PRINTING AND COUPLING PROCESSES OF FLEXIBLE PACKAGING. THESE PROCESSES ARE CHARACTERIZED BY THE NEED TO TREAT VARIABLE AIR FLOWS TOGETHER WITH HIGH QUANTITIES OF POLLUTANTS, WHICH CAN BE REUSED IN THE PRODUCTION PROCESS.
The application in the flexible packaging industry had to provide for the identification and application of specific measures aimed at enabling the following goals:
- The achievement of the highest purification performance, through a specific sizing of the process parameters.
- The optimization of energy consumption, thanks to the identification of interesting forms of energy recovery, in the various stages of the process.
- The possibility of obtaining high purities of the recovered solvents, thanks to a final distillation plant, with multiple effects.
- The absence of aqueous waste, and the minimum content of water in the recovered solvent, thanks to the presence of several dehydration phases.
THE RESULTS ACHIEVED
The results obtained thanks to the combination of these technologies confirms the efficiency of the solution that has allowed us to achieve the following goals:
- The achievement of concentration values of pollutants emitted into the atmosphere significantly lower than the prescribed regulatory limits.
- The reuse of the recovered solvents in the production process, sufficient to eliminate the need to purchase dilution solvents, but also capable of allowing the sale of the recovered solvent in excess.
- The customer’s independence from external suppliers for the supply of dilution solvents.
- The customer’s independence from any fluctuations in the market price of the solvents to be purchased.
- Obtaining certificates for the company policy dedicated to the recovery and reuse of raw materials.
- No interference with the production processes upstream of the purification plant.